Blanking is a metal production process, during which a metal workpiece is removed from the primary metal strip or sheet when it is punched. The material that is removed is the new metal workpiece or blank.
Profile of the blank piece
A die cut edge normally has four areas.
- roll-over
- burnish
- fracture
- burr
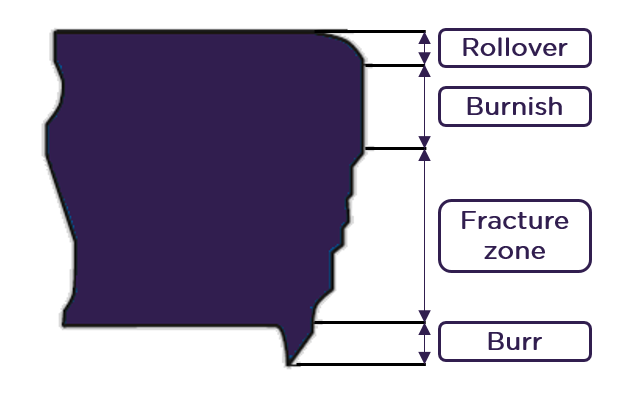
The cut surface of a cut band created with a conventional metal punching process is partially angled and has a rough appearance in the fracture zone of the cut.
During the punching/blanking operation, the working parts (punches and dies) behavior depends on the working material (thickness, tensile strengths, yield strengths) and the tool steel ability to cope with the stresses that arise on the cutting edges.
The main failure mechanism on punches and dies are :
- Plastic deformation: the permanent deformation occurs when the compression stress exceed the compressive yield strength of the tool steel. Hardness is the critical parameter.
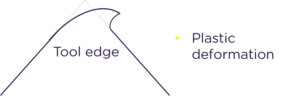
- Chipping and total breakage: both cracks initiation and cracks growth are deleted by high tool steel ductility/toughness. The very fine and homogeneous Powder Metallurgy tool steel microstructure gives to the tools the good level of impact strength and fatigue limit in case of brittle behavior.
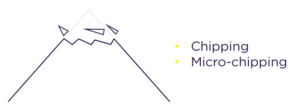
- Abrasive wear: abrasion appears on the sliding contacts between the tool and the working material. Abrasive wear is caused by hard particles in contact with the tool surface. The critical tool steel properties are hardness, high volume of carbides and high hardness of the carbides.
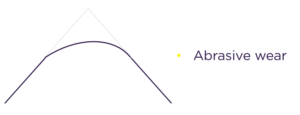
- Galling and adhesive wear: both galling and adhesive wear are created by compressive stresses and sliding contact resulting in heavy friction and locally high temperature which can lead to micro-welds spots that destroy the surface quality of the tool. Then, due to the working stresses, parts of stick material are pulled out of the tool surface by the work material. The critical parameters are roughness, friction coefficient, toughness/ductility and hardness. The tool steel grade has a big influence and Powder Metallurgy tool steels can offer the suitable solution, together with surface coating in order to optimize the sliding properties.
Moreover, when punching or blanking of advanced high strength sheet metals, stresses and shock waves increase a lot on the cutting edges of the tools. In such cases, the use of conventional tools steels (D2 andEvoloop® M2 types) is not recommended due to the too low fatigue strength / impact strength level, which lead to early cracks and total breakage of punches and dies. Chipping and cracking are probably the most detrimental failure mechanism that can occur in the production plant.
With the Powder Metallurgy process, the microstructure of the ASP® tool steels is much refined with a very even distribution of finer primary carbides. This results in an improved combination of toughness, strength and hardness in comparison to conventional tool steels.
Our ASP® cold work tool steels (Powder Metallurgy) provide a very efficient response when the limits of conventional material are exceeded.
Our standard Powder Metallurgy program was launched many years ago and has been successfully introduced and implemented all over the world in the cold work applications.
More recently, Erasteel has developed a new generation of Powder Metallurgy tool steels specially designed to offer a very good combination of wear resistance and ductility.
Advanced tooling materials from Erasteel, the Powder Metallurgy tool steels, can provide the outstanding mechanical properties needed during the production of medium/long series and avoid stoppages of the press lines.