Drilling is a well-known machining operation in which the tool, often a multi cutting edge tool, is fed into the work piece while rotating in order to make a hole. As the cutting action happens along the entire cutting edge of a drill, the cutting speeds will vary from the rotational speed of the tool at the edge to zero at the centre. This makes it impossible to have optimized cutting parameters along all points of contact and the centre of the drill will push the metal instead of cutting it.
ASP® for Drills
High-Speed Steel drills are typically made in traditional grades (Evoloop® M2, Evoloop® M35 and Evoloop® M42) manufactured by conventional metallurgy, but for drills that require higher performance the properties of Powder Metallurgy that ASP® offers are more suitable. ASP® can be used to increase tool life, allow for machining in otherwise too unstable conditions or to machine difficult materials. As ASP® drills allow for higher feed rates they can even outperform carbide drills in some operations and will offer more chipping resistance.
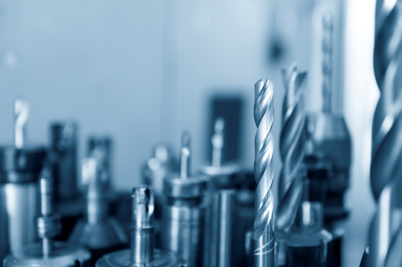
R&D - Drills
The research and development team at Erasteel continues to develop new grades of both Evoloop® and ASP® to address many different markets. For drilling there are new developments ongoing that will increase the cost effectiveness of the “Do it yourself” drill market. These new developments include new alloying concepts that allow maintaining mechanical properties, while at the same time reducing the cost of the material itself, allowing for cheaper tools without any loss of performance.
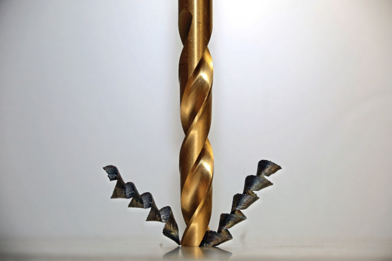
Drill applications include:
- twist drills
- micro drills
- centre drills
- starting drills
- coolant fed drills
- spade drills
- core drills
- countersinks
- counterbores
Grades | Applications | Features |
---|---|---|
Drilling in hard and tough materials | High wear resistance and hot hardness | |
General high performance drills | Good combination of hardness and toughness |
|
Evoloop® M2 | General drills | Low cost and baseline |