Erasteel is a major global player in the High-Speed Steels market and has built its reputation thanks to the high performance and quality of its products.
Addressing technical, environmental and strategic challenges, Erasteel is the partner of the most demanding industries: automotive, motorsports, aeronautics, electronics, energy, construction, high value-added tooling industries.
Thanks to its innovative approach, Erasteel has developed a range of products with a low carbon footprint while delivering exceptional performance and durability : Evoloop®
In June 2024, Erasteel becomes the world’s first producer of High-Speed Steels to obtain EPD® (Environmental Product Declaration) certification for its conventional High-Speed Steel range Evoloop®. demonstrating its commitment to a more sustainable and transparent industry regarding its environmental footprint.
Evoloop® offers the perfect fusion of innovation, performance, and preservation of natural resources and the environment:
- A low carbon footprint, from 2 to 4 times lower compared to the alternative solutions
- Products made from over 91% recycled materials and 100% recyclable
- A high level of quality and performance
- A lifetime of tools up to 10 times longer than some standard steel solutions
Conventional High-Speed Steels Specifications
High-Speed Steels (HSS) are alloys with the ability to machine materials at high cutting speeds. They are complex iron-base alloys of carbon, chromium, vanadium, molybdenum, or tungsten, or combinations thereof, and in some cases substantial amounts of cobalt. The carbon and alloy contents are balanced at levels to give high attainable hardening response, high wear resistance, high resistance to the softening effect of heat, and good toughness for effective use in industrial cutting operations.
Our conventional High-Speed Steels products, are manufactured with the conventional steel’s melting processing which includes ingots solidification, forging or rolling, heat treatments and final quality inspections.
Process and Main characteristics

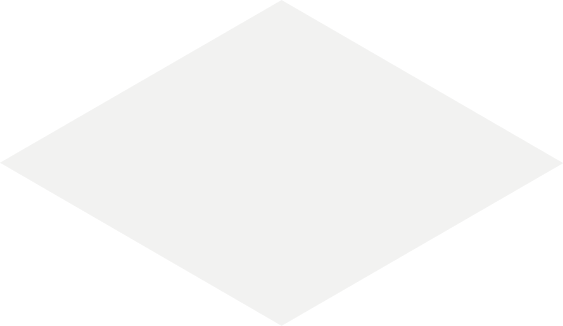
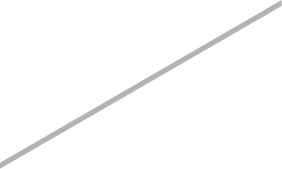
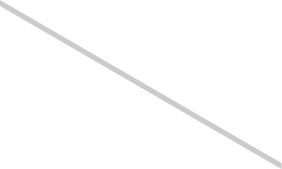
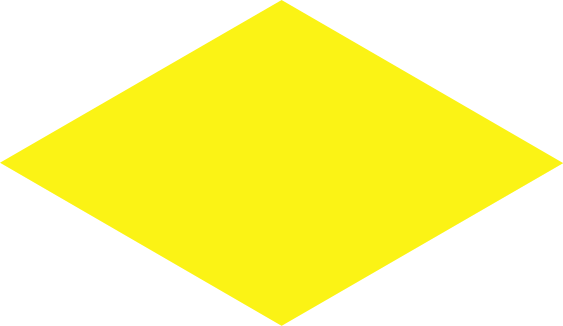
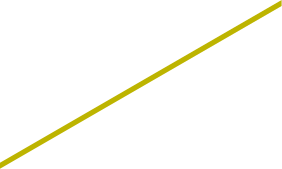
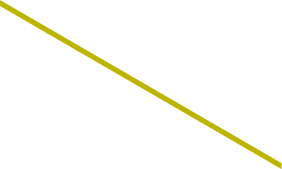
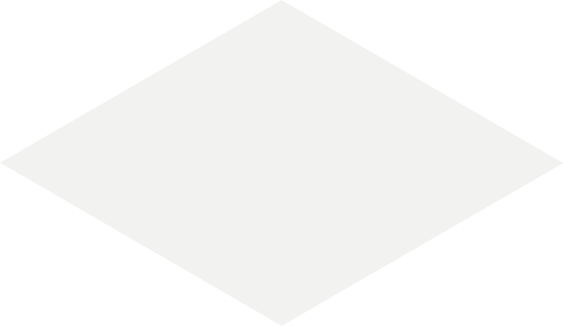
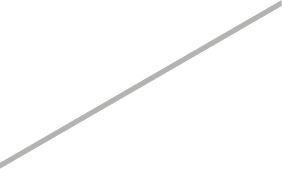
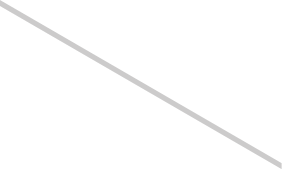
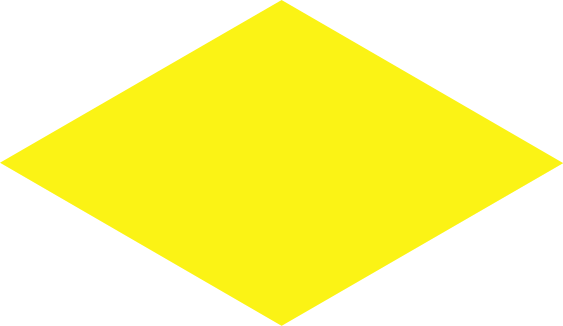
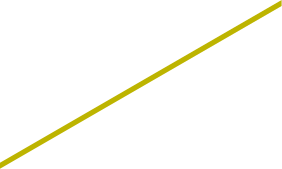
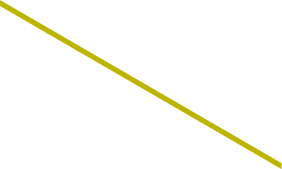
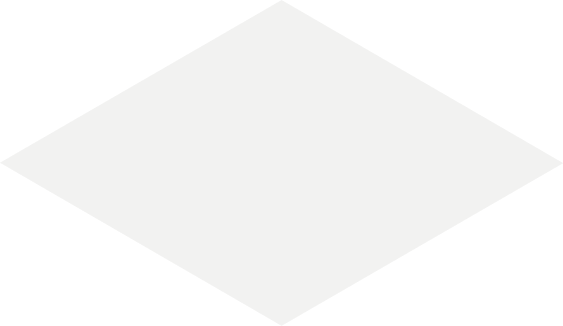
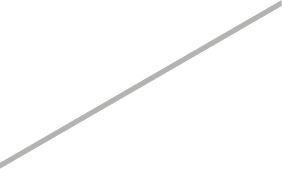
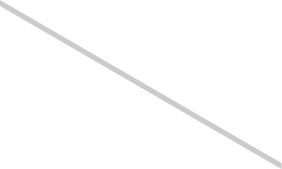
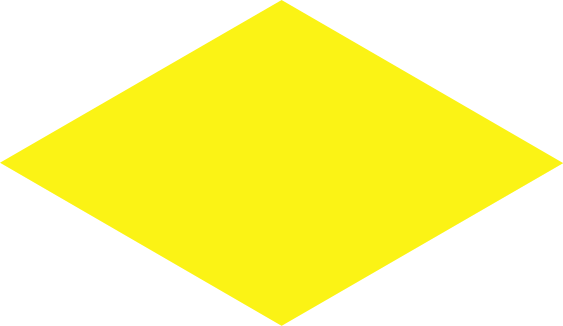
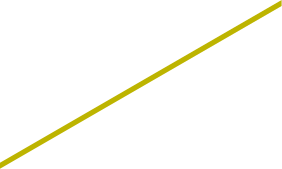
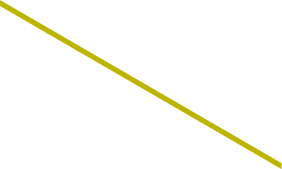
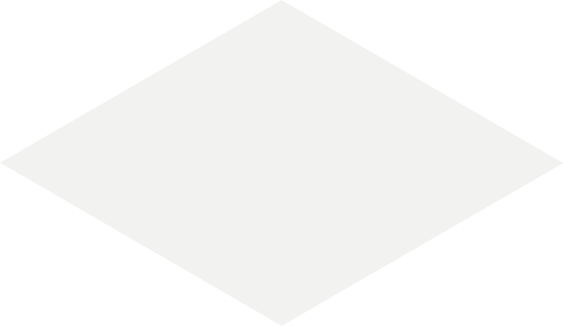
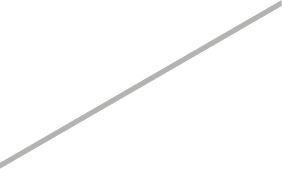
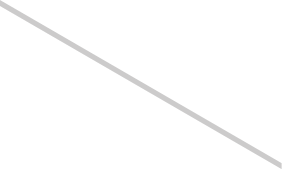
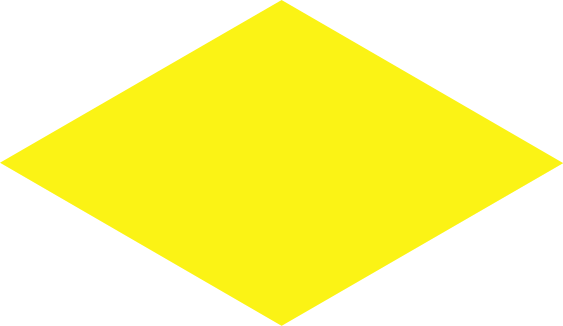
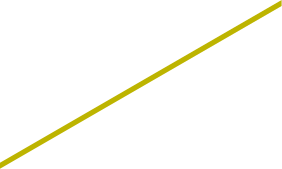
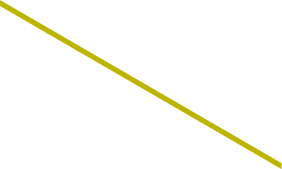
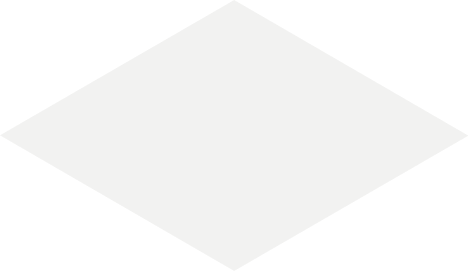
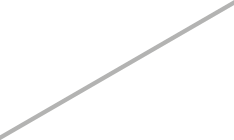
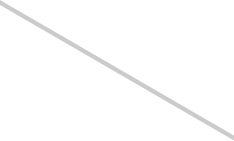
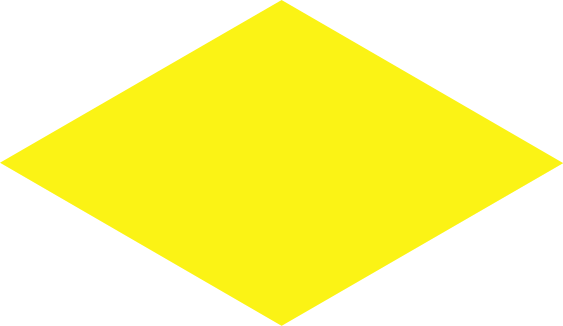
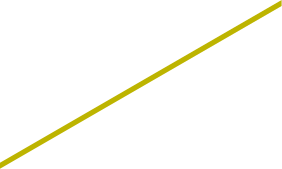
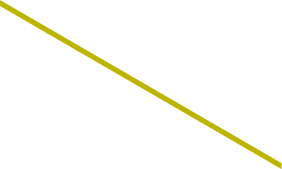
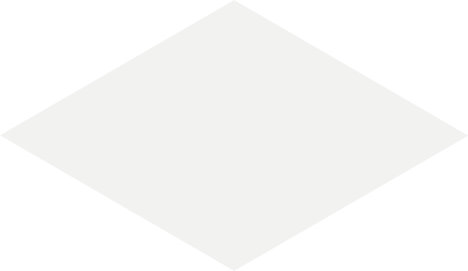
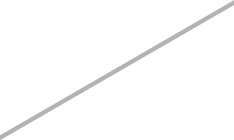
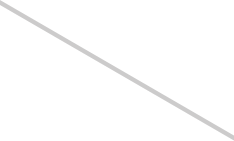
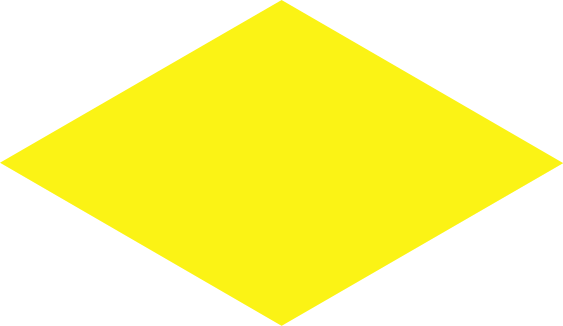
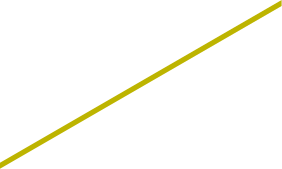
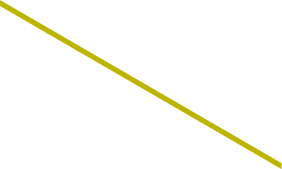
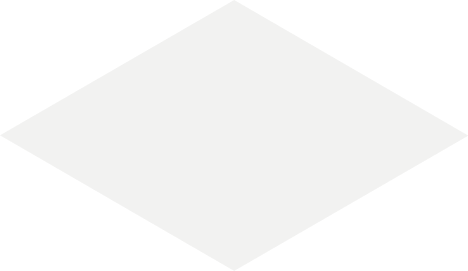
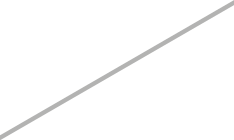
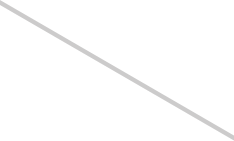
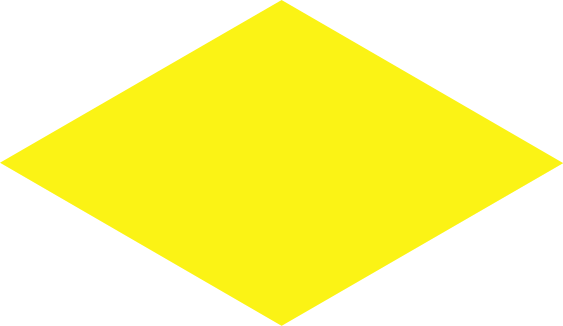
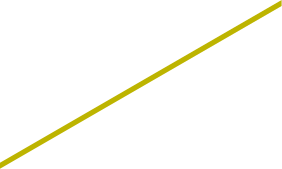
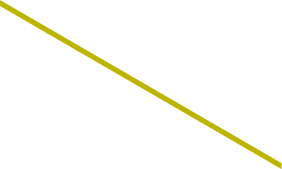
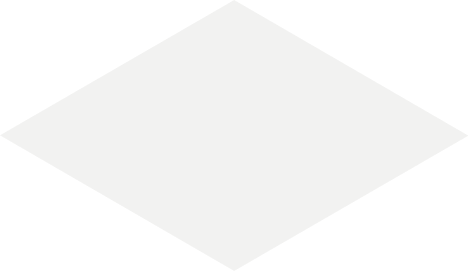
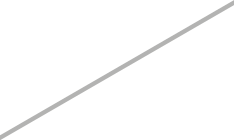
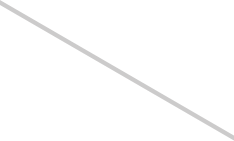
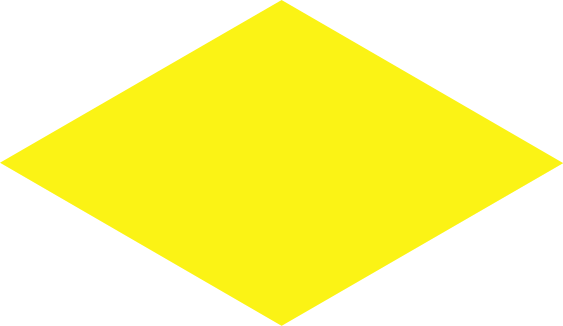
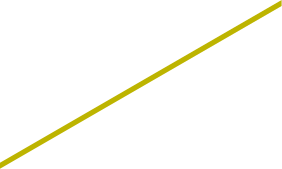
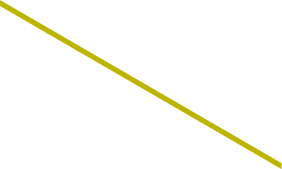
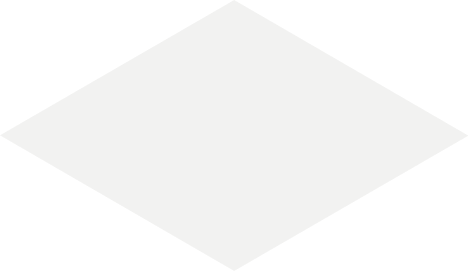
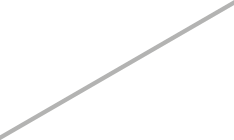
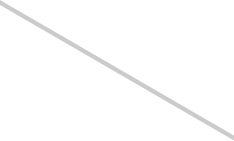
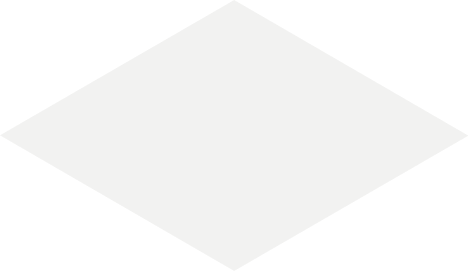
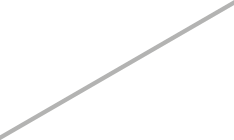
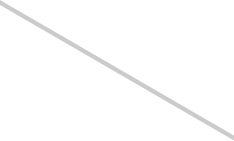
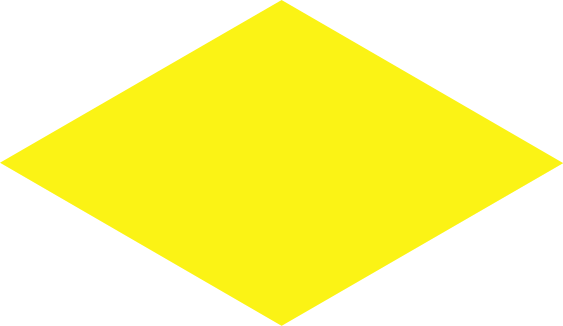
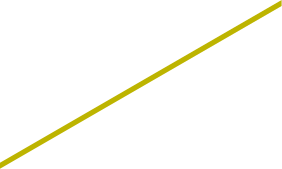
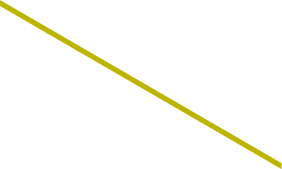
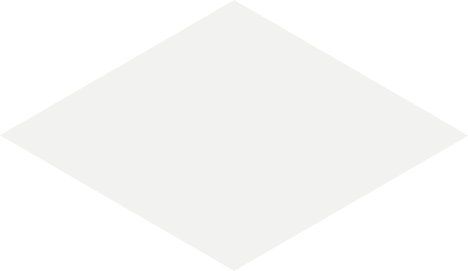
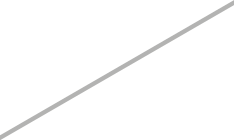
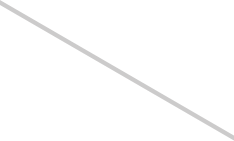
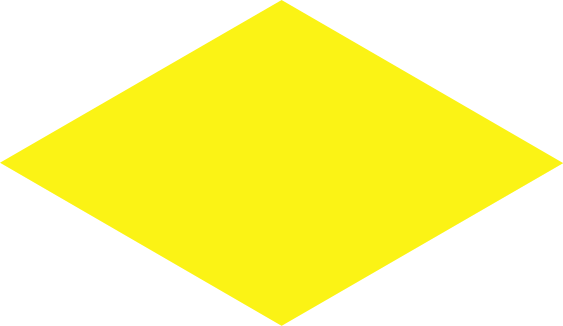
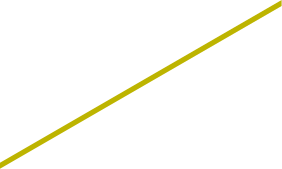
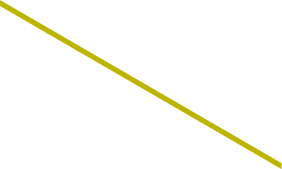
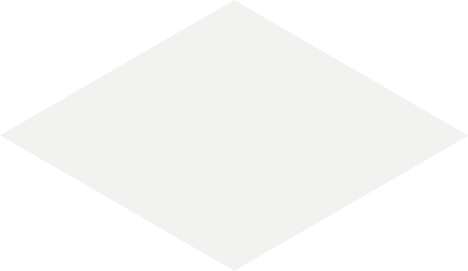
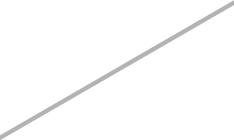
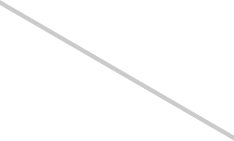
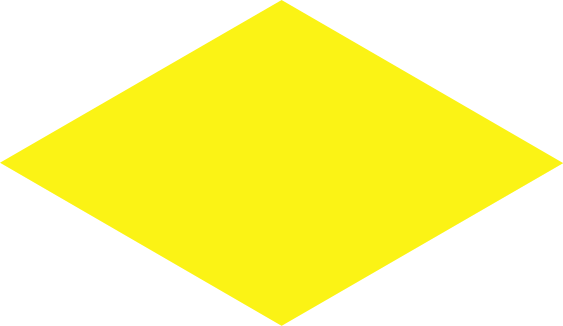
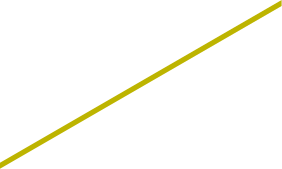
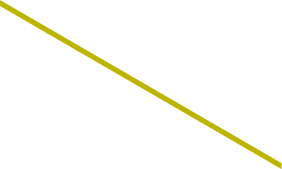
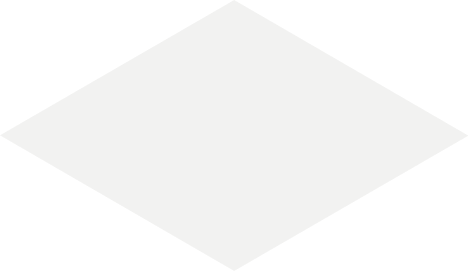
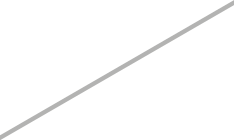
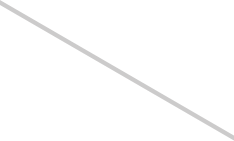
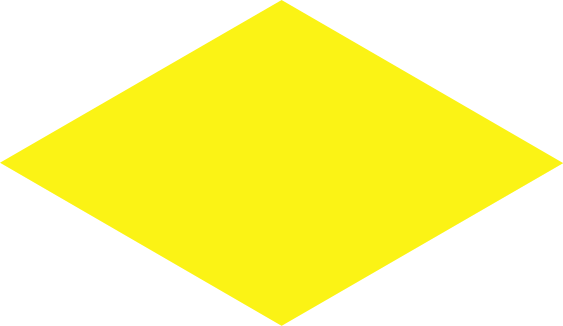
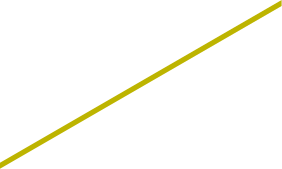
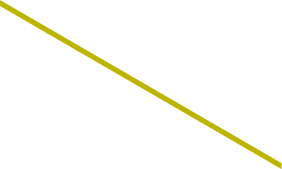
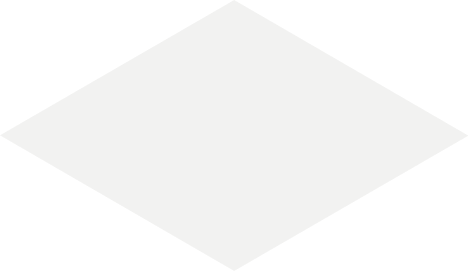
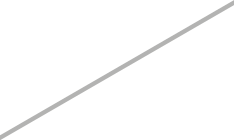
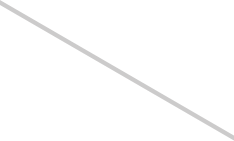
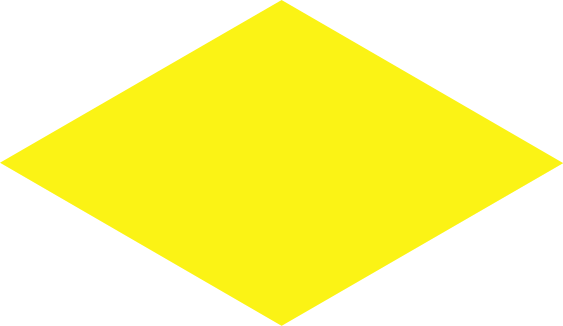
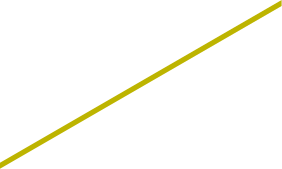
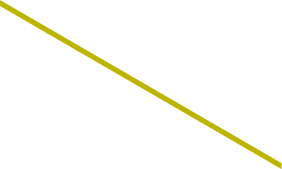
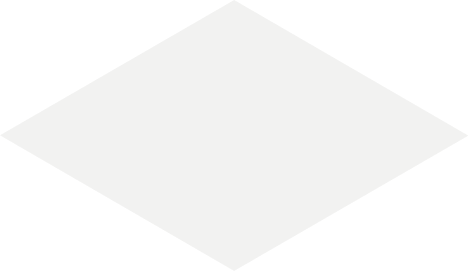
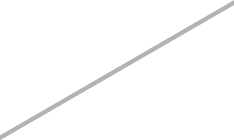
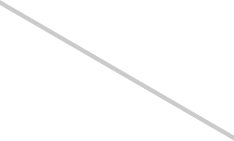
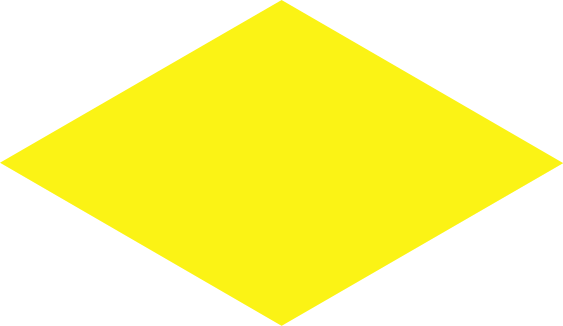
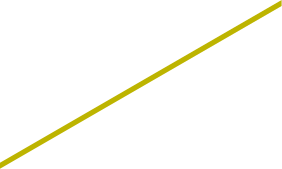
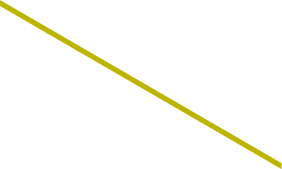
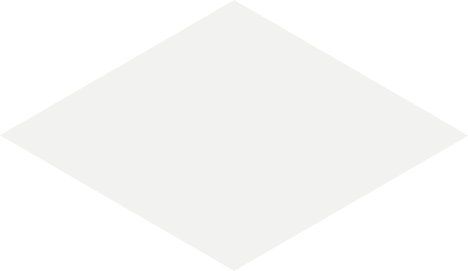
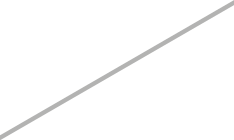
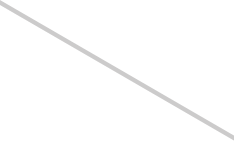
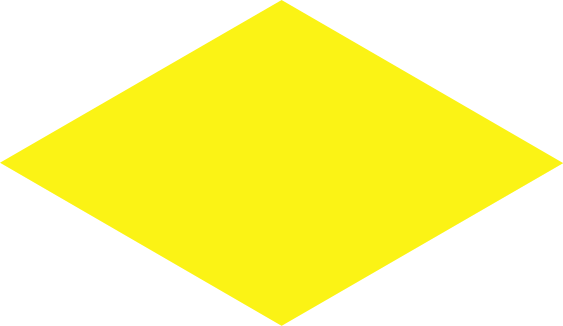
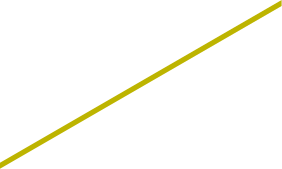
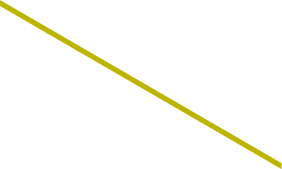
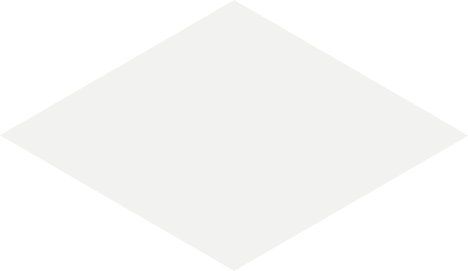
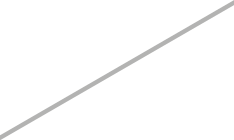
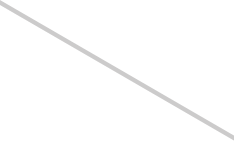
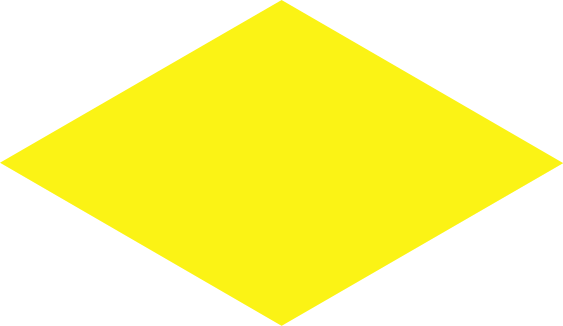
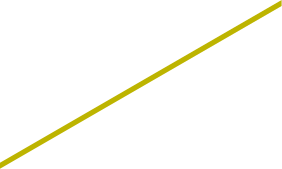
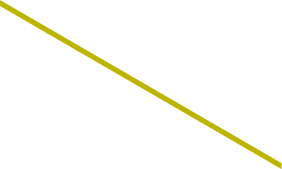
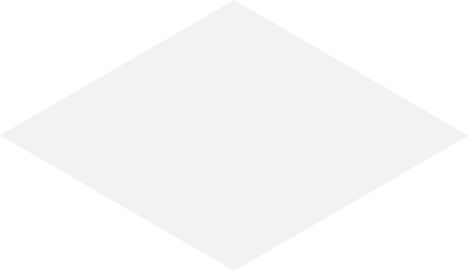
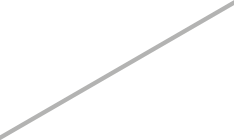
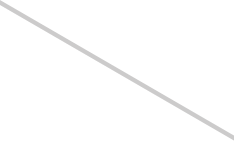
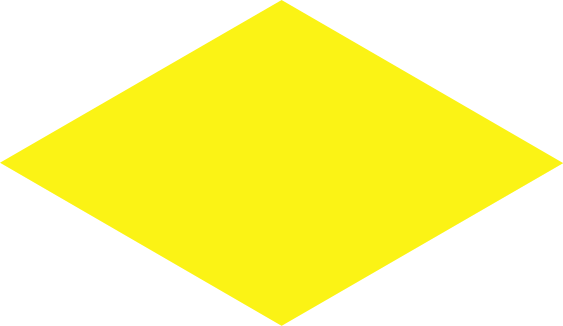
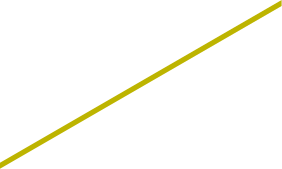
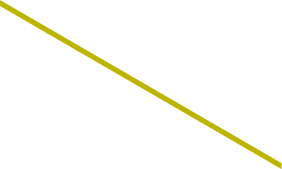
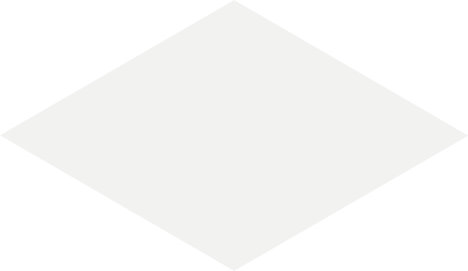
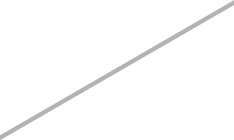
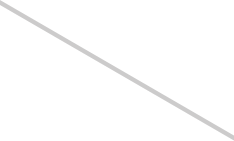
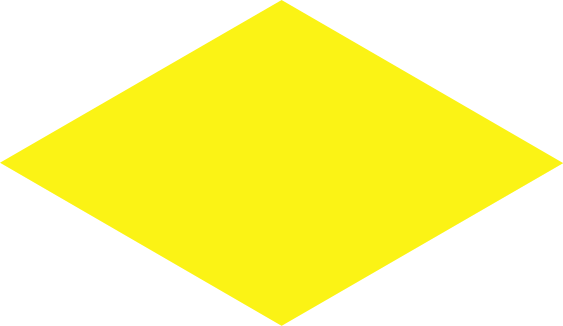
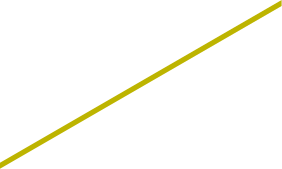
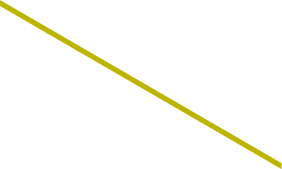
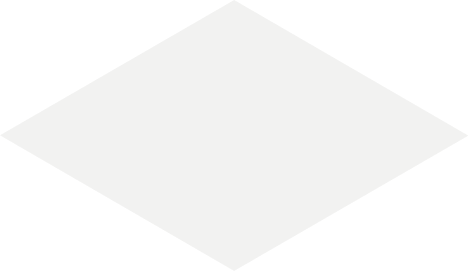
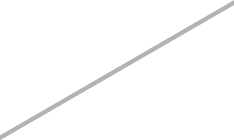
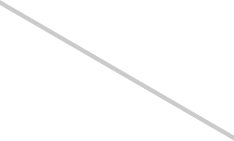
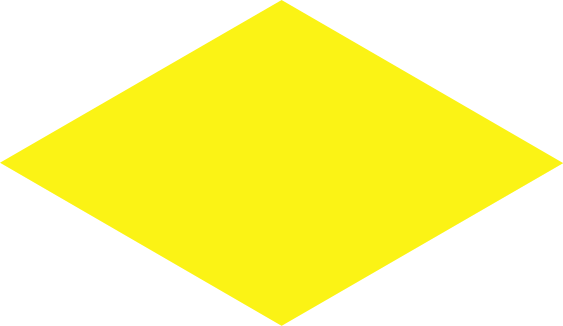
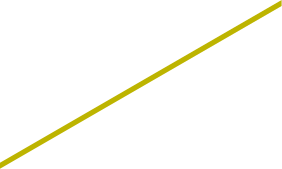
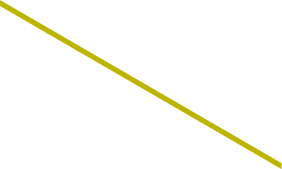
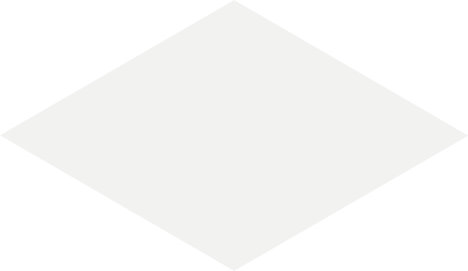
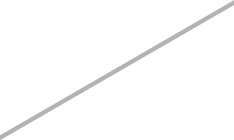
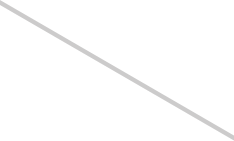
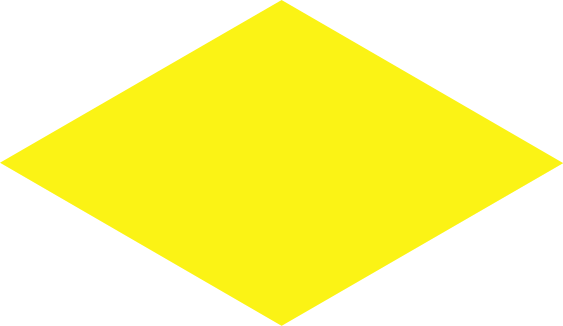
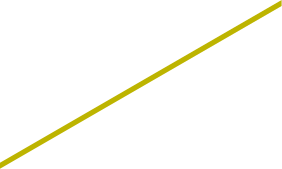
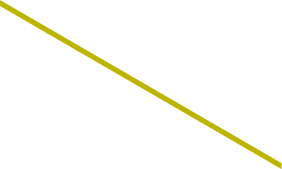
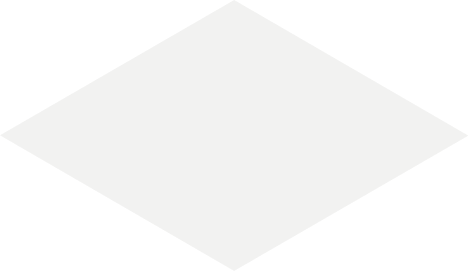
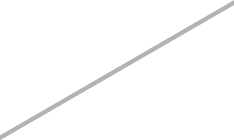
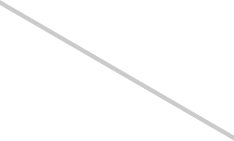
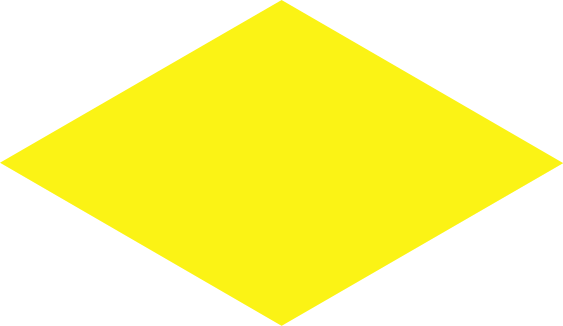
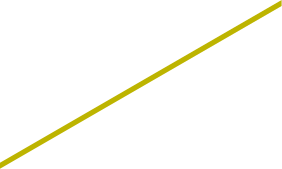
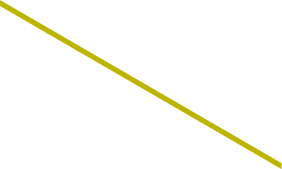
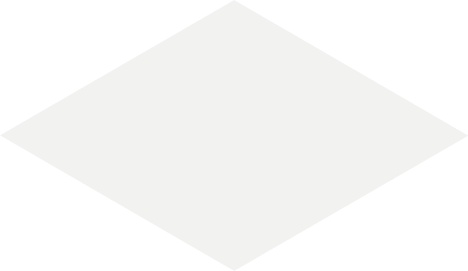
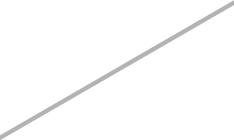
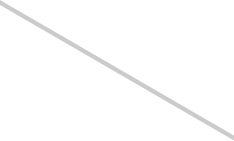
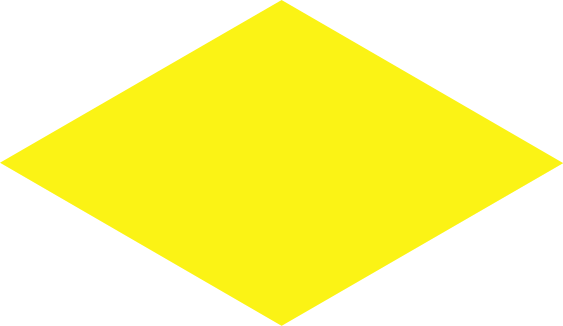
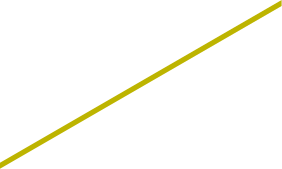
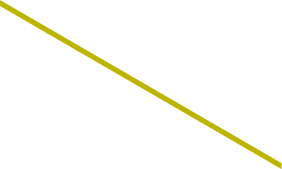

High-Speed Steels resist to wear thanks to carbides in the steel. Structural stability at up to 560°C gives High-Speed Steel a great resistance to softening. High-Speed Steel exhibit high resistance to deformation as a result of a high hardness. As the High-Speed Steel owns a high strength, they resist to breakage. For all these reasons, High-Speed Steels are suitable for tools and special components.
The Heat treatment process is as critical to the success of the cutting tool as material selection itself. Often the highest-quality steel made into the most precise tools does not perform because of improper heat treatment. The object of the heat treating or hardening operation is to transform a fully annealed high-speed tool steel consisting mainly of ferrite (iron) and alloy carbides into a hardened and tempered martensitic structure having carbides that provide the cutting tool properties. Heat treatment of High-Speed Steel is done in salt bath or in a vacuum furnace. High quality for High-Speed Steels is also comes from the quality of the heat treatment.
Evoloop® High-Speed Steels grades
Erasteel, through its brand Evoloop®, offers a large range of conventional High-Speed Steels with or without cobalt as:
HSS COBALT FREE
- Evoloop® M2 for general applications included rolls
- Evoloop® ABC III for metal saws and wear parts
- Evoloop® Grindamax™V3 with excellent grindability
- Evoloop® M4 with high wear resistance for cold forming and rolls
HSS WITH COBALT
- Evoloop® M35 grade for general applications
- Evoloop® C8 for end mills and milling cutters, a High Co-alloyed grade with high hot hardness and high wear resistance
- Evoloop® MAT II for bi-metal saws with good thoughness
- Evoloop® M42 for cutting tools and bi-metal bandsaws